The Role of a Squeeze Film Damper
Vibration Control
Rotating equipment requires damping to control vibrations and prevent them from damaging the rotor, bearings and other components.
While fluid film bearings provide a significant amount of damping, it may not be sufficient for all rotating machinery. An additional means of increasing “effective” damping may be needed.
A squeeze film damper is a layer of film between the bearing and the housing that softens the bearing support to increase damping effectiveness. This film is in addition to the hydrodynamic film between the bearing and the shaft.
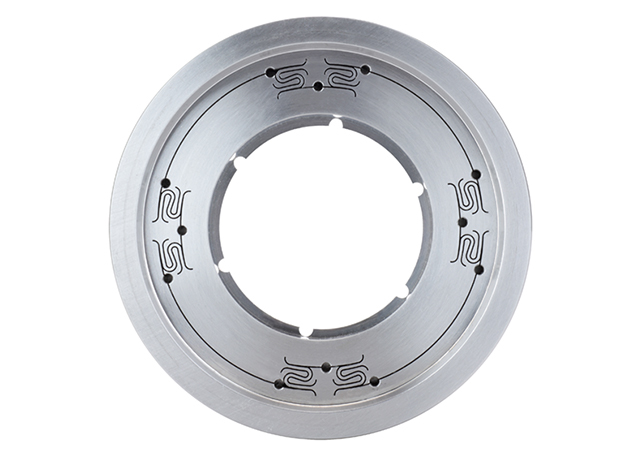
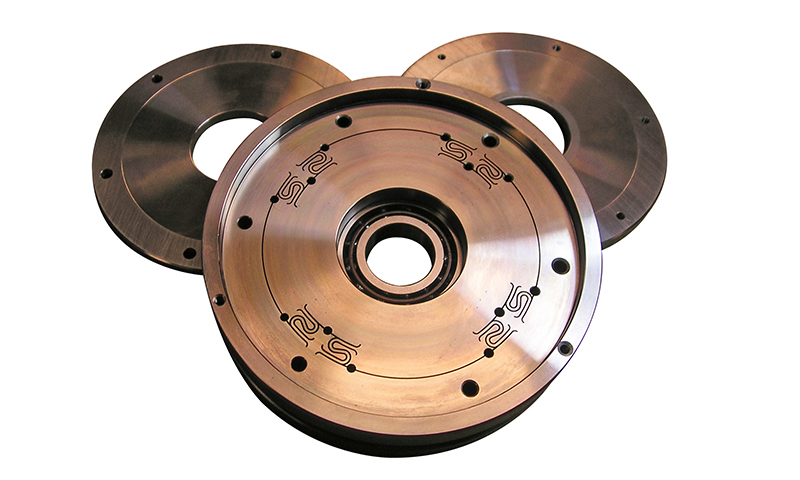
Squeeze Film Damper Benefits
The result of using an engineered damper can be:
- Increased stability
- Reduced rotor response
- Increased separation margin between operating speed and critical speeds
- A reduction in forces transmitted from rotor to ground
- Reduced pedestal vibrations
- Reduced bearing wear
- Decreased sensitivity to changes to the rotor, such as material buildup on a rotating component
Squeeze film dampers are typically used on high-speed machinery and/or with a flexible rotor.
Conventional Squeeze Film Dampers
A conventional squeeze film damper generates damping by squeezing oil in the damper film.
The damping is governed by the circumferential film flow, which makes it difficult to control oil flow resistance and create non-linear damping. The damper’s performance can also be affected by vibration amplitude and frequency.
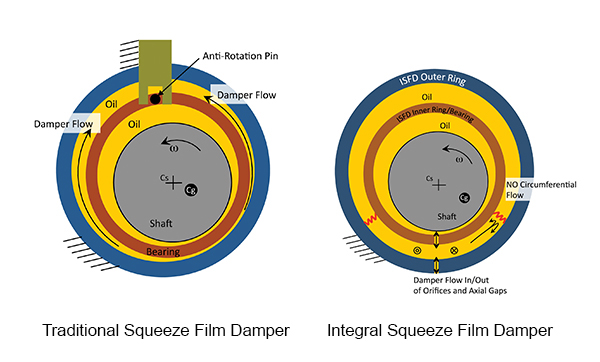
Integral Squeeze Film Dampers
ISFD® technology from Waukesha Bearings provides more precise control of the damping, as well as the stiffness.
The segmented ISFD design prevents circumferential flow and controls damping by flow resistance at the oil supply nozzle. It absorbs energy more like a shock absorber.
Stiffness of the ISFD design is defined by integral “S” shape springs, allowing for better predictability and precise placement of critical speeds and rotor modes.