Fluid Film Bearings
Optimized Performance
At Waukesha Bearings, we collaborate with customers to engineer hydrodynamic fluid film bearings for optimized performance in individual operating conditions.
In addition to properly sizing bearings to handle the required loads and minimize power loss, we expertly apply surface geometries, tilt pad designs, lubrication methods, materials and other specialized features to achieve peak performance. The result is an endless variety of customized fixed profile and tilt pad bearing systems.
No matter how challenging the turbomachinery, our engineers have the knowledge and application experience to design the right solution.
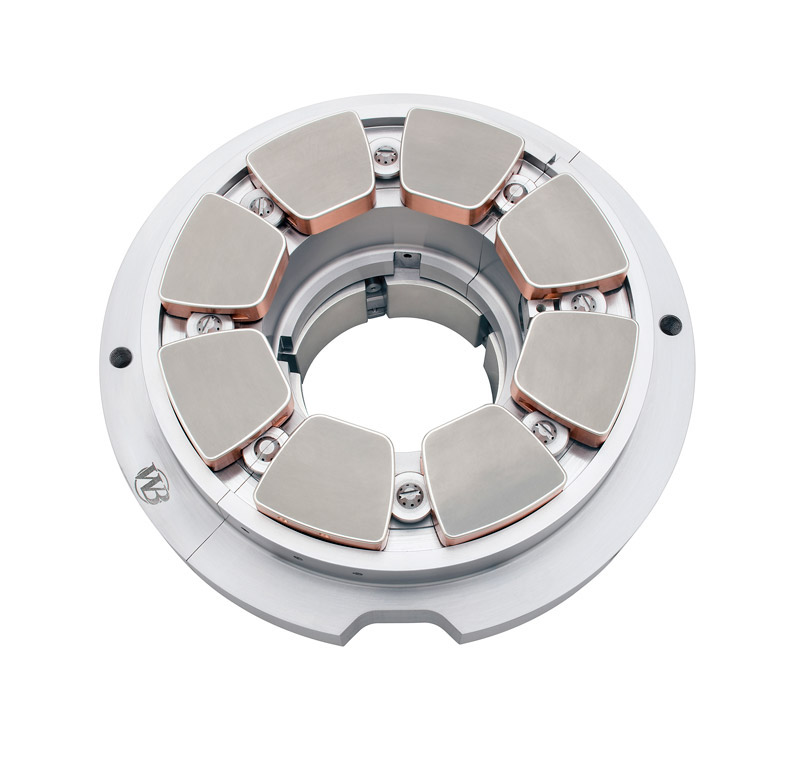
Thrust (Axial) Bearings
Vertical Assemblies
Horizontal Assemblies
Comprehensive Rotordynamic Analysis
Through rotor modeling and a full evaluation of equipment operating conditions, Waukesha Bearings can simulate critical speeds, rotor modes, undamped natural frequency and unbalance response, among other characteristics.
Rotordynamic analysis tools are combined with bearing coefficients from in-house design programs to provide highly accurate analyses and predictions for the validation of original builds and the design of optimized solutions.
Engineered Damping for Vibration Control
Rotating equipment requires damping to control vibrations and prevent them from damaging the rotor, bearings and other components. While fluid film bearings provide a significant amount of damping, it may not be sufficient, particularly for machinery running at high speeds and/or with a flexible rotor. The system may require an increase in “effective” damping.
Waukesha Bearings ISFD® technology provides highly engineered damping and stiffness to shift critical speeds and increase the dynamic stability of the rotor/bearing system.
Advanced Materials for Advanced Performance
Materials play a significant role in bearing performance, and continuing materials development has expanded the ability to meet stringent application goals, such as increased load capacity, reduced power loss, or operation in process fluids.
Waukesha Bearings applie advanced materials, including polymers, ceramics, cermets and aluminum tin, to extend the operating limits of fixed profile and tilting pad bearings.
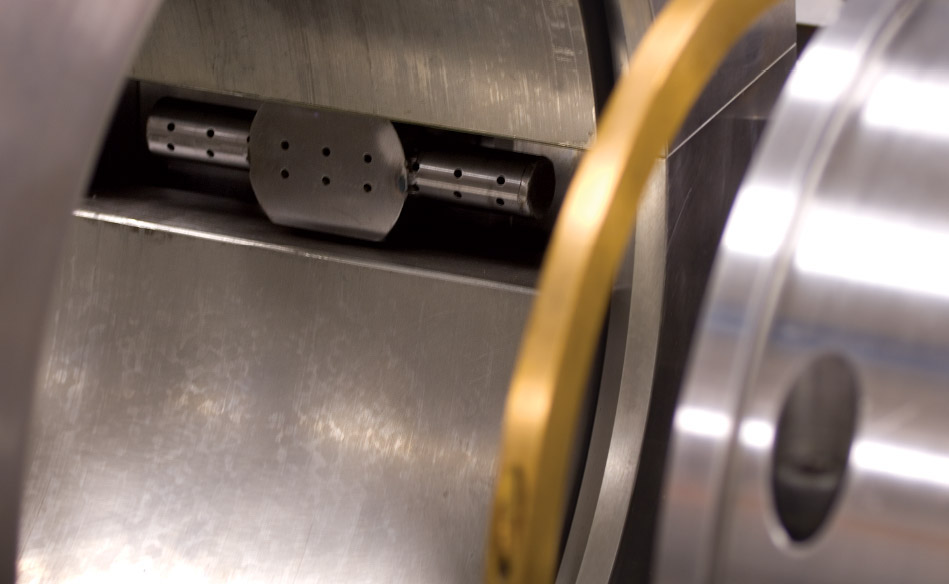
Waukesha Bearings Advantage
- Experience with challenging and mission-critical applications
- Unmatched engineering expertise and materials knowledge
- Global reference list with leading OEMs
- Patented and proprietary design features
- Design and manufacture to extreme tolerances
- Extensive testing and validation
- Proprietary, field-proven prediction programs
Backed by R&D
As more demands are placed on your equipment, you need a partner with the right technology to support you. Waukesha Bearings is committed to ongoing technology leadership and is investing now to ensure we can deliver the solutions you need for the future.
How Fluid Film Bearings Work
When properly designed and maintained, the working life of a fluid film bearing is theoretically infinite. Under these circumstances, contact between bearing surfaces and the rotor occurs only at start-up and in the final stages of rundown. During operation, the rotor moves on a continuous film of oil, water or other filtered process fluid.