TruTech® Polymer Bearings
Increase Bearing Capacity
Initially used as a high-performing substitute for metallic linings, engineered polymers now provide increased bearing capacity and reliability for a wide variety of rotating equipment.
Polymers combine higher strength at elevated temperatures and higher fatigue strength while maintaining the embeddability and conformability of babbitt.
With these properties, polymer-lined and solid polymer components can serve as direct replacements for babbitt components or be incorporated into new designs to extend operating limits.
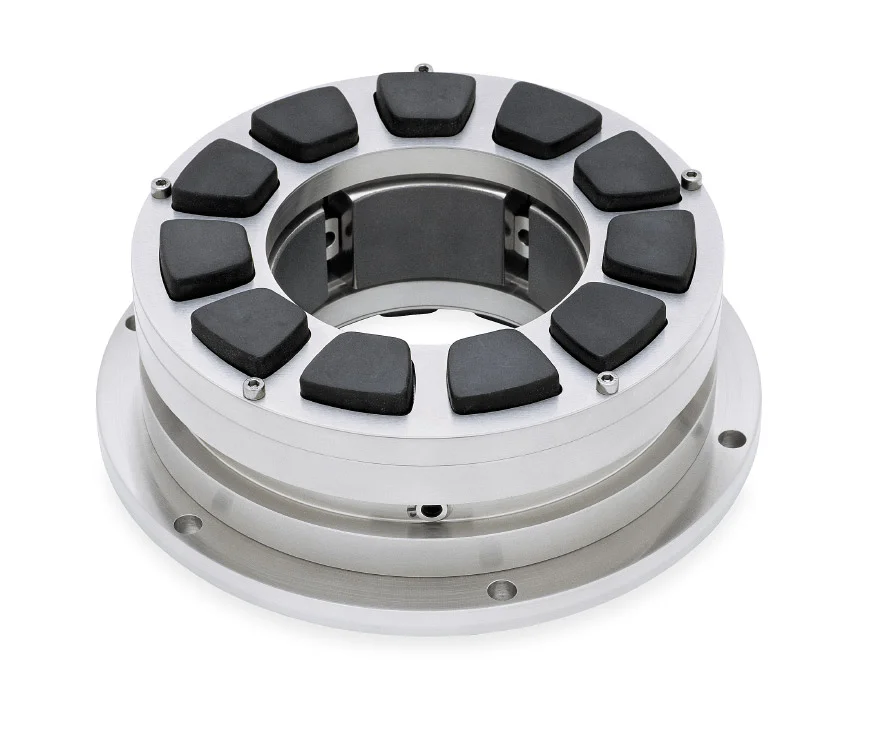

TruTech Engineered Polymers
Incorporating the latest advances in polymer science, TruTech materials from Waukesha Bearings provide superior durability and optimum performance characteristics for fluid film bearings. Custom proprietary formulations are developed and tested fully in-house to provide lasting reliability for even the most demanding applications.
Dover Precision Components Materials Development Program
The Dover Precision Components Materials Technology program integrates materials research with extensive engineering resources and more than a century of practical experience to develop next-generation polymeric materials and ensure the ongoing quality of our raw materials.
Broad in-house research and development capabilities enable us to control development from material composition through the manufacturing process and product testing. We comprehensively analyze and test materials at our advanced materials lab for physical, thermal, and wear patterns. Next, materials are incorporated into bearing products and tested in real-world conditions at the state-of-the-art Dover Precision Components Innovation Lab. Finally, materials are factory and field tested by OEMs before they are qualified for an application.
This, combined with deep engineering expertise, allows us to select the right material for the right application based on a multitude of parameters such as temperature, load, speed, lubricants, and chemistries present within the application.


TruTech Engineered Polymers Deliver Benefits Over Babbit
Higher Temperature Capability
Polymer materials have higher operating temperature capabilities – up to 250°C (482°F) – and retain their mechanical properties at higher temperatures than babbitt, allowing exceptional performance at elevated temperatures.
Embedability
Polymers, in a similar way to babbitt, will embed dirt that enters the fluid film, preventing damage to the journal or collar.
Operation with Challenging Lubricants
Advanced materials are compatible with even the most challenging lubricants and process fluids, including mineral/synthetic oils, water/seawater, water-glycol, freon, toluene, amine, crude oil, hydrocarbon condensates, liquid O2, liquid CO2, methane, propane, butane, and hexane.
Corrosion Resistance
Engineered polymers are resistant to most chemicals, including hydrogen sulfide and ammonia. This prevents bearing damage associated with chemical attack by the working fluid.
Reduction of Start-up Torque
Polymer bearing materials have a lower coefficient of friction than babbitt and can be used to reduce torque and wear at start-up, eliminating the need for hydrostatic lift systems in some applications.
Thinner Hydrodynamic Films
Surface properties and the mechanical strength of engineered polymers allow bearings to operate with thinner films than traditional babbitt bearing materials, providing:
- High load capacity – up to 10 MPa (1500 psi)
- Reduced power loss – up to 30% savings
- Operation with low-viscosity lubricants
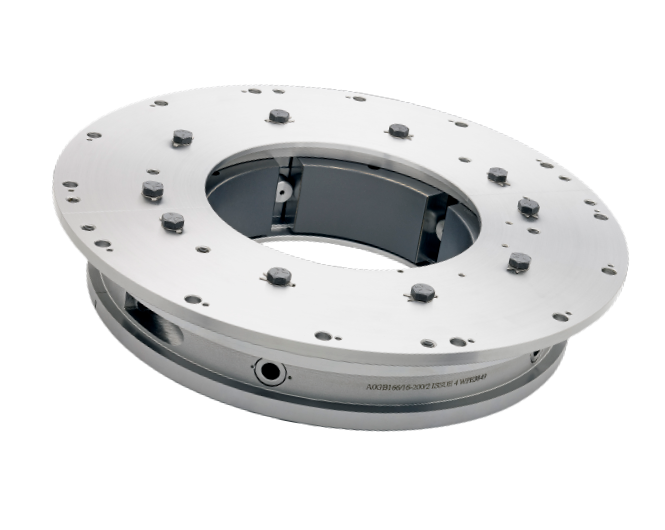
Typical Applications
Oil Lubrication
Subsea Pumps and Motors
Polymer-lined thrust and journal bearings, widely used in multi-phase booster pumps and water injection pumps, operate on very thin hydrodynamic films to meet the demand for high load capacity and long life.
Gas Turbines
Polymer-lined tilt pad thrust and journal bearings can replace babbitt bearings to withstand high temperatures resulting from heat soak. This high-temperature capability provides additional safety in the event the back-up lubrication system fails or can even eliminate the need for a back-up system, saving on both weight and cost.
Electric Submersible Pumps (ESPs)
Polymer-lined tilt pad thrust bearings are the standard for ESP operating temperatures up to 200°C (392°F) and loads up to 8 MPa (1160 psi). They are used in the motor to account for thermal expansion and in the seal/protector section to withstand the pump load. As an additional benefit in the motor, the bearings provide electrical insulation.
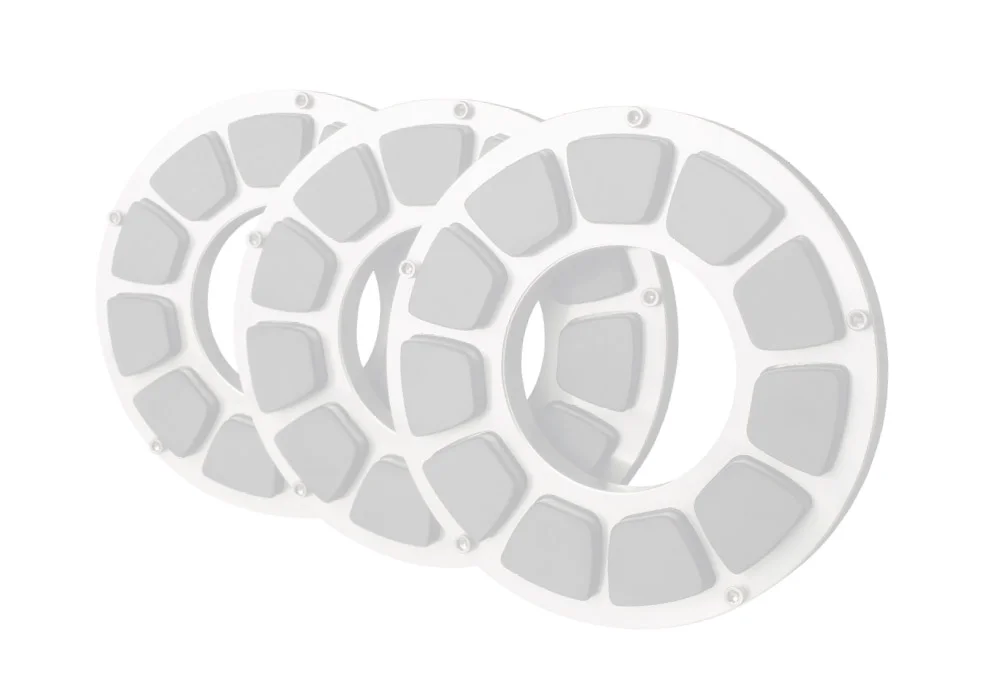
Water or Process Lubrication
Pumps
Polymer bearings can use process fluids as the lubricant, requiring fewer seals in a pump and eliminating the need for a separate oil lubrication system. Solid polymer bearings provide a solution for load capacities up to 10 MPa (1500 psi) in clean water and have been used successfully in reverse osmosis pumps, boiler feed pumps and mine-dewatering pumps.
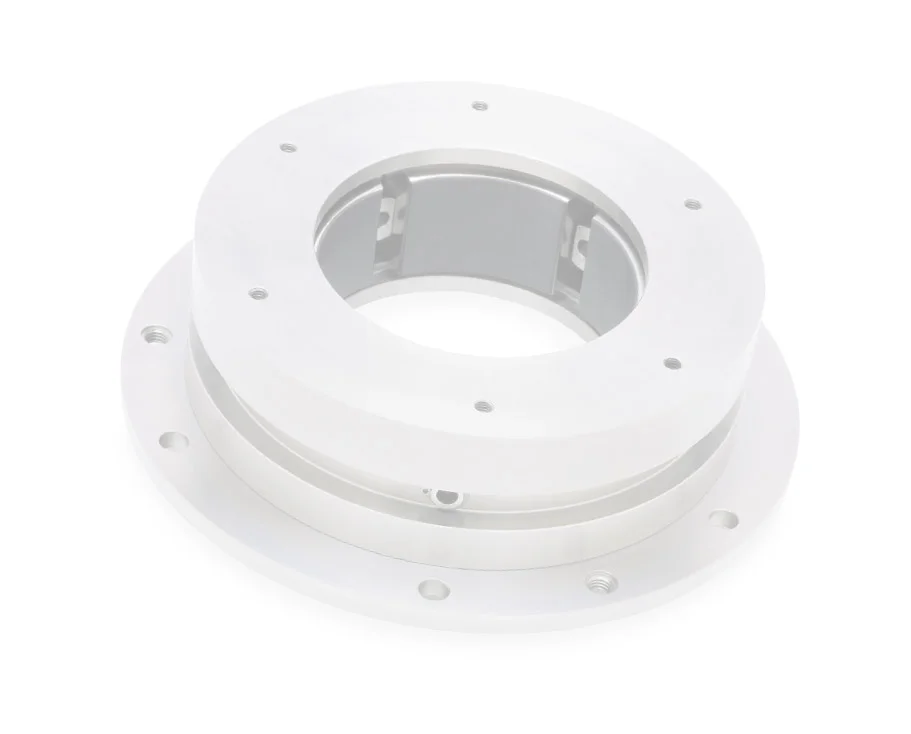
Organic Rankine Cycle (ORC) Turbines
ORC turbines use solvents such as toluene and hexane as both the working fluid and the lubricant for the bearings. Polymer journal and thrust bearings can sustain the thin films associated with these low-viscosity fluids. The sealing and the flow path of the lubricant are key design considerations for successful operation.
Water-Filled Motors
Thrust bearings with polymer surfaces support high pump loads in water-filled motors and are lubricated by the water cooling the motor.
Water-Lubricated Compressors
Using polymer bearings with water lubrication in compressors eliminates oil contamination of the compressed product and simplifies the sealing components.