News
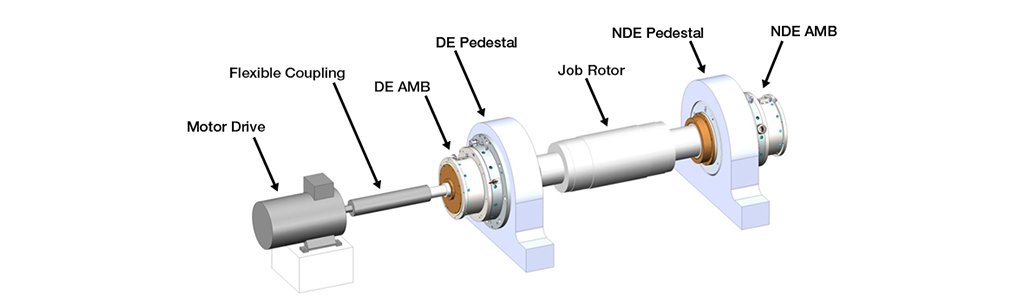
Efficient Balancing of Active Magnetic Bearing-Supported Rotors
Shafts of high-performing rotating equipment experience a certain mass unbalance distribution resulting from manufacturing tolerances, component assembly and material nonhomogeneities. The residual unbalance generates uneven forces on the rotor as it spins, resulting in vibrations and the transfer of dynamic loads to the bearings and supporting structure.
To limit the negative effects of rotor vibration, ISO and API standards set balancing criteria and acceptance levels for residual rotor unbalance. Whether magnetic or fluid film bearings are used in the machine, there is a prerequisite for spinning a rotor to its rated speed. The rotor must be balanced to meet an acceptable residual unbalance level.
The ability of an active magnetic bearing (AMB) system to tolerate high levels of unbalance on the rotor by applying unbalance force rejection control algorithms does not alter the balancing requirements. Rotors supported by AMBs and rotors supported by fluid film bearings are subject to the same balancing requirements.
In the June 2016 issue of COMPRESSORtech2, Andrea Masala of Waukesha Magnetic Bearings discusses the options and considerations in performing low- and high-speed balancing of active magnetic bearing-supported rotors. Two case studies are also discussed.
Read the article in the print or digital edition of the magazine (subscription required), or download a PDF version below.