News
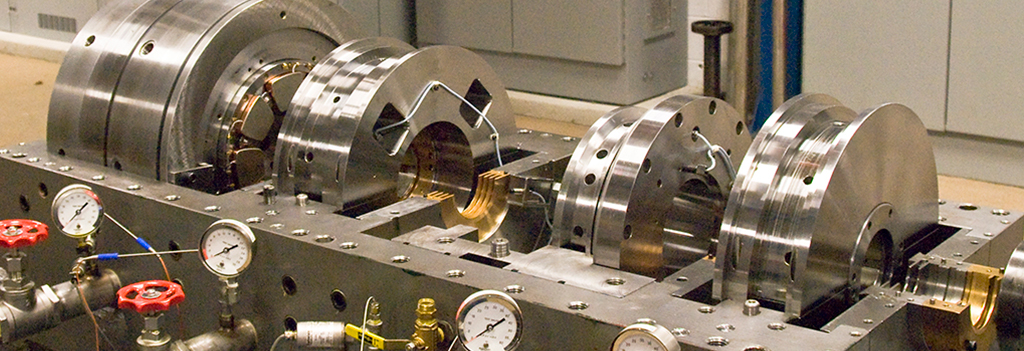
Waukesha Bearings Co-authors Paper with Ansaldo Energia for 62nd ASME Turbo Expo
“A System Integration Approach for Heavy-Duty Gas Turbine Upgrades Using Improved Rotor Thrust Predictions and Application of Advanced Thrust Bearing Designs,” a joint paper by Ansaldo Energia and Waukesha Bearings, will be presented at the ASME Turbo Expo in Charlotte, North Carolina, Wednesday, June 28 at 8 am (Session 15-1, in room 207D).
Authors
Francesco Bavassano, Ansaldo Energia; Marco Mantero, Ansaldo Energia; Riccardo Traverso, Ansaldo Energia; Richard Livermore-Hardy, Waukesha Bearings; Barry Blair, Waukesha Bearings
Abstract
The progressive upgrading of heavy-duty gas turbines, aimed at increased performance, can ultimately introduce more onerous operating conditions, to the point that original design limits can be approached.
An increased gas turbine pressure ratio together with compression and expansion line adjustments can directly affect the rotor axial thrust. Other than the individual forces acting on the rotor, a key component to be taken into account is the fluid film thrust bearing, which should assure safe and reliable operation during the worst case operating conditions.
Typically, such bearings are designed with large safety margins, yet it is possible that the new and more challenging conditions require a bearing capability upgrade, especially when field retrofit needs pose additional constraints.
A succession of performance upgrades have been carried out on Ansaldo Energia’s AE94.2 E-Class GT. An accurate understanding of the thrust-related phenomena proved necessary and drove improvements in the thrust bearing design along with hardware adjustments to lower the rotor thrust.
This paper addresses calculations and experimental arrangements for the rotor axial thrust evaluation on the aforementioned GT and considers both the matters related to the secondary air system for the thrust generation and the mechanical/functional matters for the bearing upgrade. It is shown that issues such as uneven load sharing across the thrust bearing, or the variability of rotor thrust from engine to engine within the fleet, strongly affect the maximum thrust assessment and thus the requirements used in the process of selecting a suitable bearing.
A predictive calculation method is described considering the main thrust contributions. Field experimental setups and main observations are reported. Measurements have been carried out using thermocouples and load cells placed on many of the thrust bearing pads. Moreover, the engine cavities carrying the highest and/or the most uncertain thrust share have been instrumented and characterized by pressure sensors.
The development of an upgraded thrust bearing is finally depicted through the main issues addressed, such as improved thrust pad lining material, increased load sharing efficiency and enlarged thrust bearing active surface area. Waukesha Bearings test results on the upgraded lining material, a high-tin aluminium alloy, are reported as well.
A multidisciplinary approach is presented as necessary to manage the crucial challenge of improving the thrust balancing system, especially in the case of a formerly designed engine which receives a powerful upgrade.