Brush Seals
Increase Operational Efficiencies
Compliant brush sealing systems from Waukesha Bearings can be applied to a wide variety of rotating equipment in air, steam, or process gas applications to reduce the leakage gap between the sealing surface and rotor.
The compliancy of a brush seal allows the bristles to deflect with minimal wear, thereby maintaining a small leakage gap over time and increasing operational efficiencies.
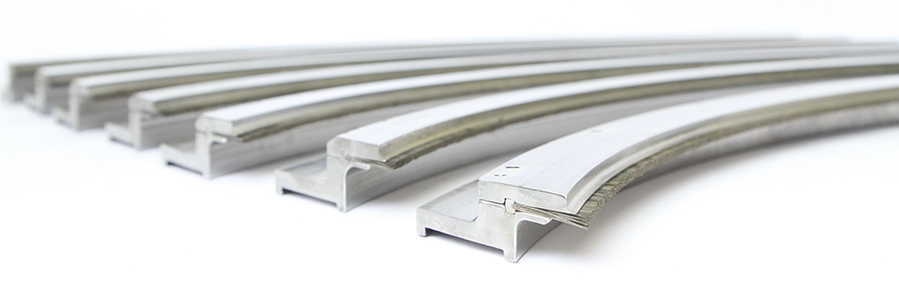
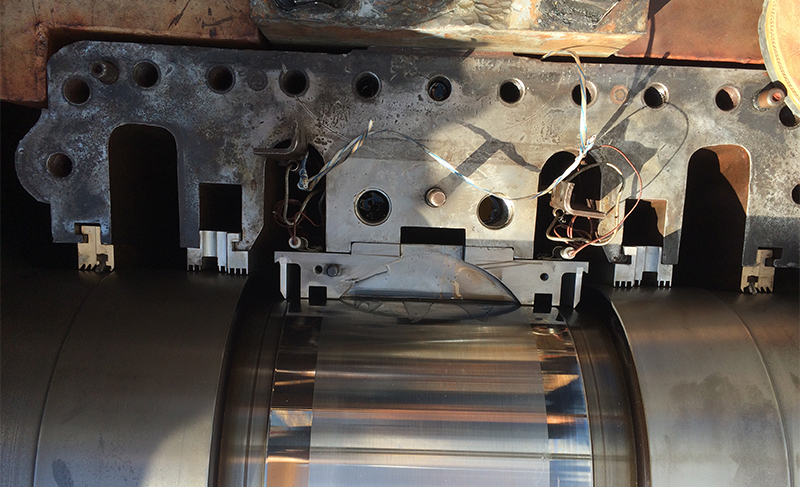
Valuable Savings
The uniqueness of our product rests with its flexible sizing and replaceable bristle pack. These two features alone are technology differentiators and provide the benefits of quick turn times, ease of installation, and seal repair.
These benefits coupled with efficiency gains provide valuable savings in solving your critical sealing needs.
Brush seals have been shown to reduce labyrinth leakage by up to 80%.
Aerospace Origins, Industrial Success
Our patented brush seal (US Patent 6,231,047) was originally developed for the aerospace industry. First installed in the 1980s in efforts to improve jet engine efficiency and reduce airborne pollutants, brush seals have since accumulated millions of successful operating hours.
Our experience has taken the technology beyond aerospace into the harsh and demanding environments of industrial turbomachinery, where we now have more than 1,600 units in operation.
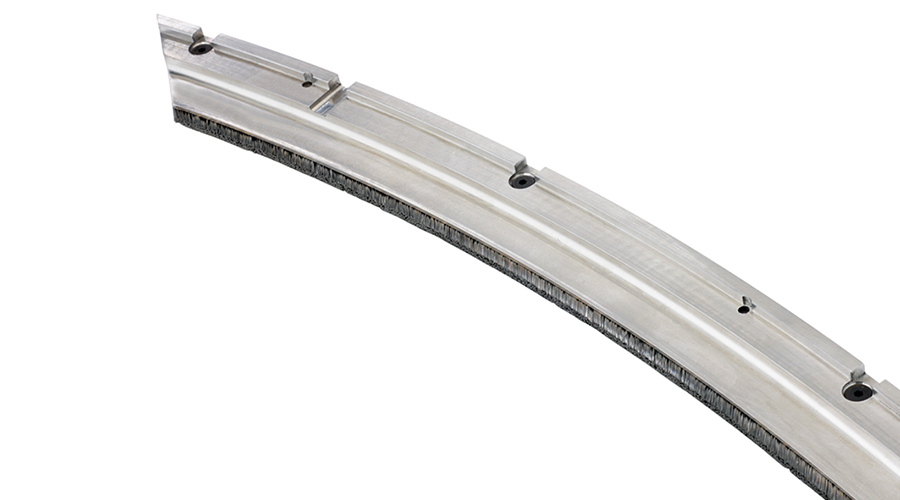
Technical Data
- Pressure: Up to 300 psid (20 bar) per row
- Temperature: Up to 650°C (1,200°F)
- Surface speed: Up to 335 m/s (1,100 ft/sec)
- Environments: gas path (air, steam); bearing (air/oil)
- Housing material: stainless steel, Inconel, others
- Bristle material: Haynes 25
- Diameter: 19 mm (0.75″) to more than 3,050 mm (120″)
- Configurations:
- Solid ring
- Split ring
- Segmented
- Cartridge
- Linear strip
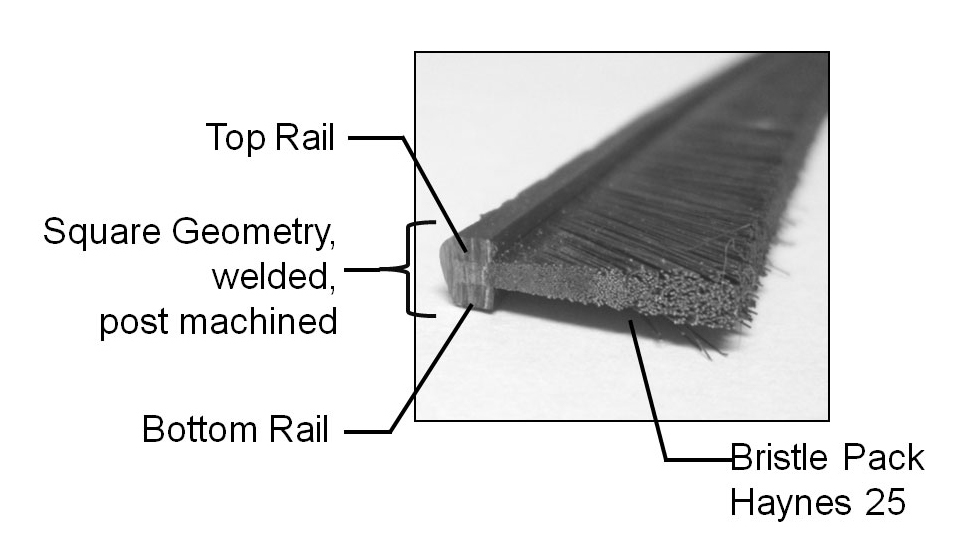
Waukesha Bearings Advantage
- Engineering expertise to analyze complete rotor-bearing system dynamics
- Installation list of more than 1,600 units
- Lasting efficiency gains
- Low-profile design
- Flexible sizing
- Modular assembly for up to 30% reduction in replacement costs
- Easy to install
- Quick turnaround times